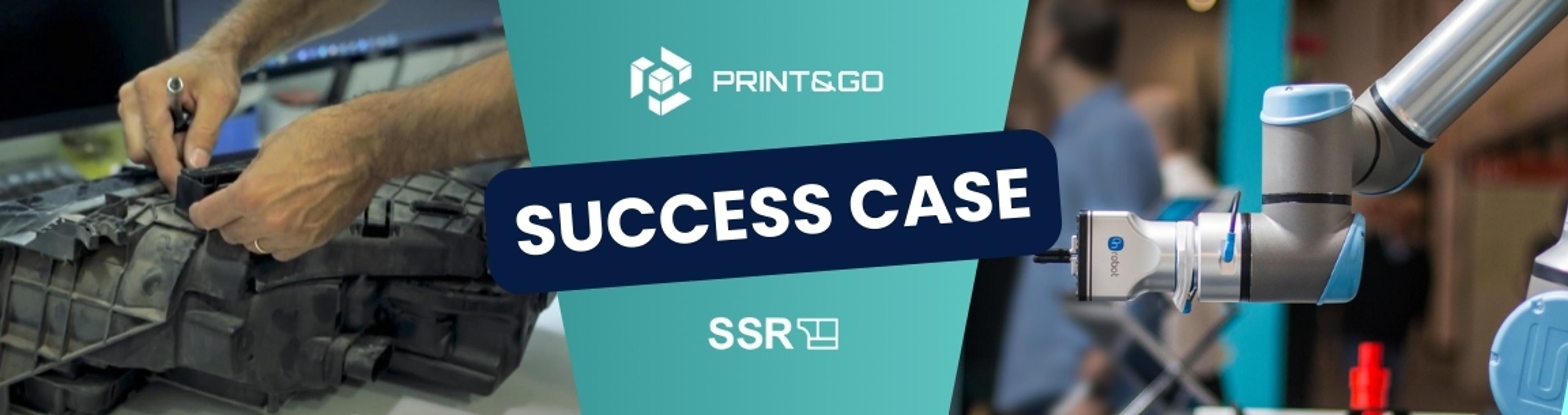
Success case: Speed Service Reparation
At Print&Go, we are focused on making easy, autonomous 3D printing a reality. That is why we have partnered with Speed Service Reparation to elevate their 3D printing workflow and position them at the forefront of the automotive repair industry.
About Speed Service Reparation
Speed Service Reparation is a leading repair company of automotive plastics with many years of experience.
Their commitment to always achieve the best results has enabled them to rely on the latest technologies, improving their production processes and drastically reducing turnaround times.
Project's requirements
Speed Service Reparation approached Print&Go to overcome the challenge of fully automating their 3D printing process. As their business expanded, they recognized the need for increased autonomy and control, particularly in managing print jobs and optimizing power usage for a more efficient production line.
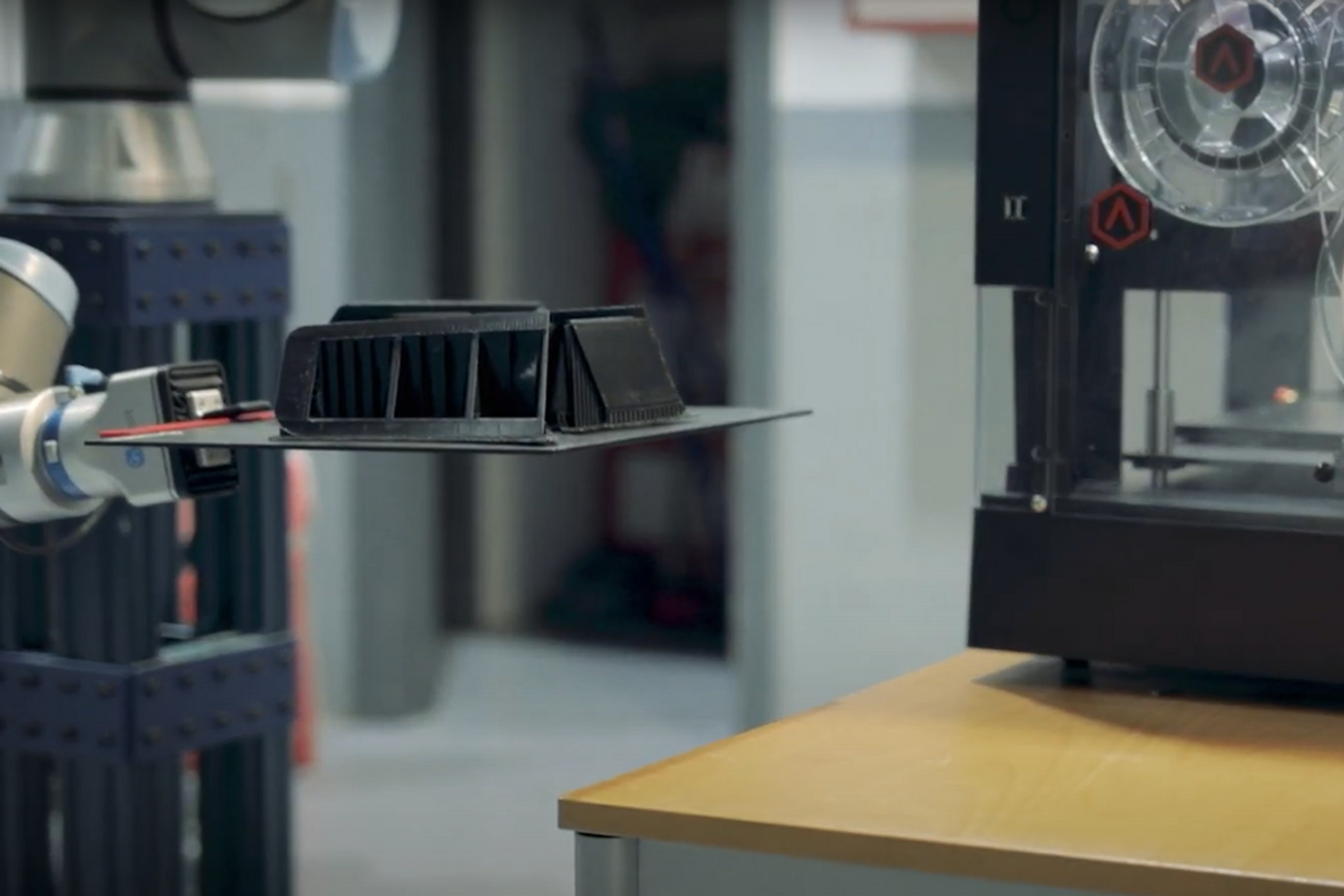
Project results
After thorough consultations and ongoing collaboration, Print&Go provided Speed Service Reparation with an advance 3D printing software and a sophisticated collaborative robotic arm (cobot). This technology aimed to revolutionize the way they handle printings by automating complex processes and giving them greater autonomy over their operations.
As a result of this integration…
- 3D printing workflow software:
This software allowed them to manage printing jobs remotely, schedule print times and detect errors early, among others. It reduces manual oversight and human errors, optimizing productivity. - Robotic arm:
It enabled the company to automate previously labor-intensive tasks like cleaning and sanding. It can now also be used in multiple areas of the repair process within the same organization, enhancing overall efficiency.
Benefits
By partnering together, Speed Service Reparation has experienced significant improvements in several areas:
- Greater autonomy:
Easily remote and centralized printing processes, reducing dependency on manual intervention. - Simplified printing process:
The software removed common 3D printing challenges, transforming the printing process into something easy. - Enhanced control over material waste:
Print&Go's system allowed precise control over material usage, reducing waste and lowering production costs. - Remote monitoring and management:
Staff can manage printing processes from anywhere, ensuring continuous workflow without the need for constant onsite supervision. - Scheduled print times:
They gain the ability to schedule print jobs, achieving better planning and workload distribution.